Hornady announced their new A-TIP match bullets about two months ago before the NRA annual meeting. But if you’re not a long-range precision shooter, the news may not have caught your eye. Another new bullet design? OK then. Yawn.
A closer look, however, reveals just how big a deal the new A-TIP Match bullet design and manufacturing process really are. Short version: A-TIPs feature a machined aluminum tip (rather than traditional polymer) and are sequentially packaged for the highest possible round-to-round consistency.
That blurb still doesn’t really do these bullets justice, though.
Long-range shooters crave one thing above all…consistency. They want to know that each bullet they send downrange is as identical in every respect to every other round they fire. That gives a precision shooter accurate, predictable results they can count on.
Until now, lots of precision shooters bought polymer-tipped bullets like, say, Hornady’s ELD Match rounds. But polymer tips have a couple of problems. First, they shrink slightly during the molding and curing process. Second, they aren’t as flexible in the kind of profiling that’s possible when they’re made.
There’s another problem, too. Testing of polymer-tipped bullets using Doppler radar revealed that polymer-tipped bullets’ ballistic coefficient changes during their flight path. This was due to the tips actually melting and deforming as they traveled.
Hornady came up with their Heat Shield Tip to address that problem years ago, but that didn’t address the issues with shrinkage and profile. The A-TIP bullets’ machined aluminum tips fix all of that.
First, since they’re turned metal rather than molded plastic, there’s zero shrinkage when they’re made. Each tip can be formed to exact, consistent standards throughout the manufacturing process. Second, aluminum can be turned to almost any length and geometry (within reason). This flexibility gave Hornady new options in terms of center of gravity and other properties that polymer tips don’t allow.
Heres’ what Hornady’s 140 grain ELD Match polymer-tipped rounds look like:
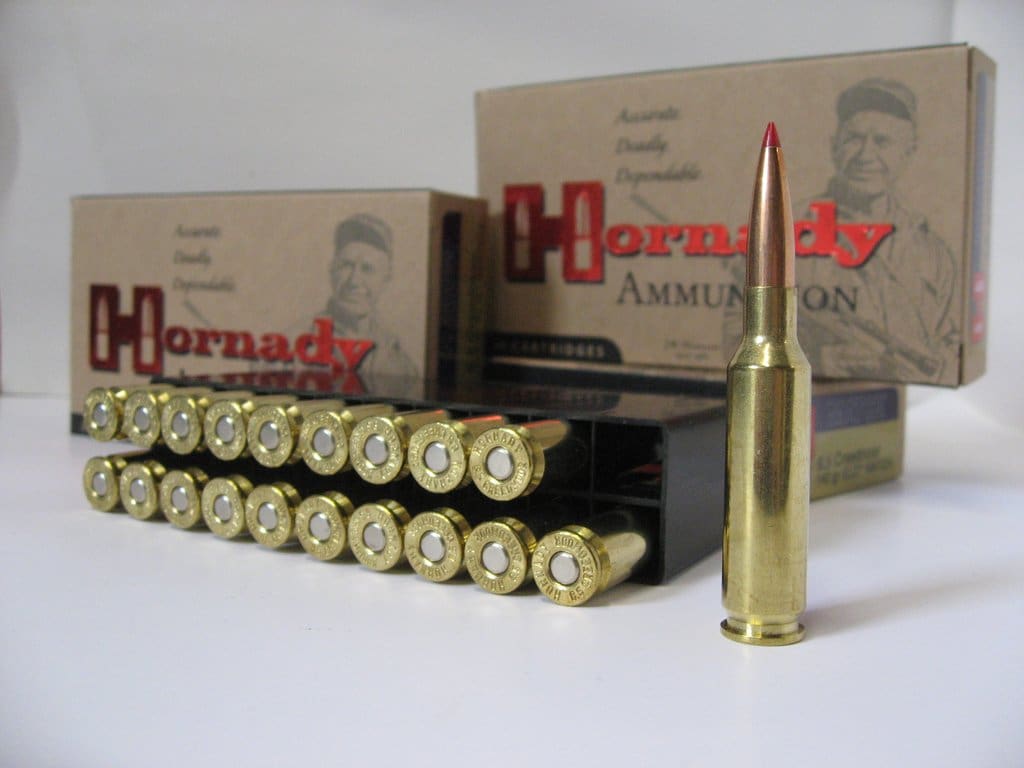
And here are 135 grain 6.5CM A-TIPs:

You can see the difference in length and geometry. That lengthened design results in lower drag coefficients (higher ballistic coefficients).
The interface between the tip and bullet is incredibly precise as well. If you run your thumbnail over the seam, you can hardly feel the transition.
So that’s what Hornady did with the A-TIP bullet’s design. Then they changed the way the bullets are packaged for what has to be the utmost in bullet-to-bullet consistency.
Most match bullets are manufactured in quantity, dropped into a bin, then scooped out for the packaging process. As a result, match bullets bought in bulk tend to vary in weight and length depending on where each was produced in a manufacturing run.
That variance may not seem like much, but to precision shooters who try to wring every bit of accuracy out of each round, it makes a difference. If you weigh a package of match bullets fresh out of the box, they will fall somewhere along a bell curve with about 75-80% in the middle, having very similar weights. The other 20-25% will fall on one tail or the other, either lighter or heavier.
Hornady, however, packages A-TIP bullets sequentially. That means far more consistency and a much flatter bell curve.
Each round is packaged as it comes off the line, one after the other. So when you buy a box of from 100 to 1000 bullets, you know they were all made in the same production run, one after the next.
Here’s the promo video Hornady made for the A-TIPs that describes them well.
A-TIP bullets aren’t tumbled or washed after they’re made, either. They may have some oil or other residue on them when the buyer gets them. That’s why Hornady packages them with a Hornady-red polishing bag to clean them before loading.
As you might imagine, all of this makes A-TIPs significantly more expensive. The cost of A-TIPs runs anywhere from 70% more to over twice as much more per bullet over comparable ELD Match bullets depending on caliber and quantity.
Hornady’s offering the A-TIPs in three calibers and five weights so far.
TTAG got a chance to spend a couple of days at Leupold’s range in central Oregon last week shooting 135 grain 6.5 Creedmoor A-TIP rounds last week.
Eight of us industry types mounted brand spanking new Leupold Mark 5HD 7-35×56 scopes on brand spanking new Ruger Precision Rifles and ranged steel with Leupold’s RX-2800 TBR/W rangefinders.
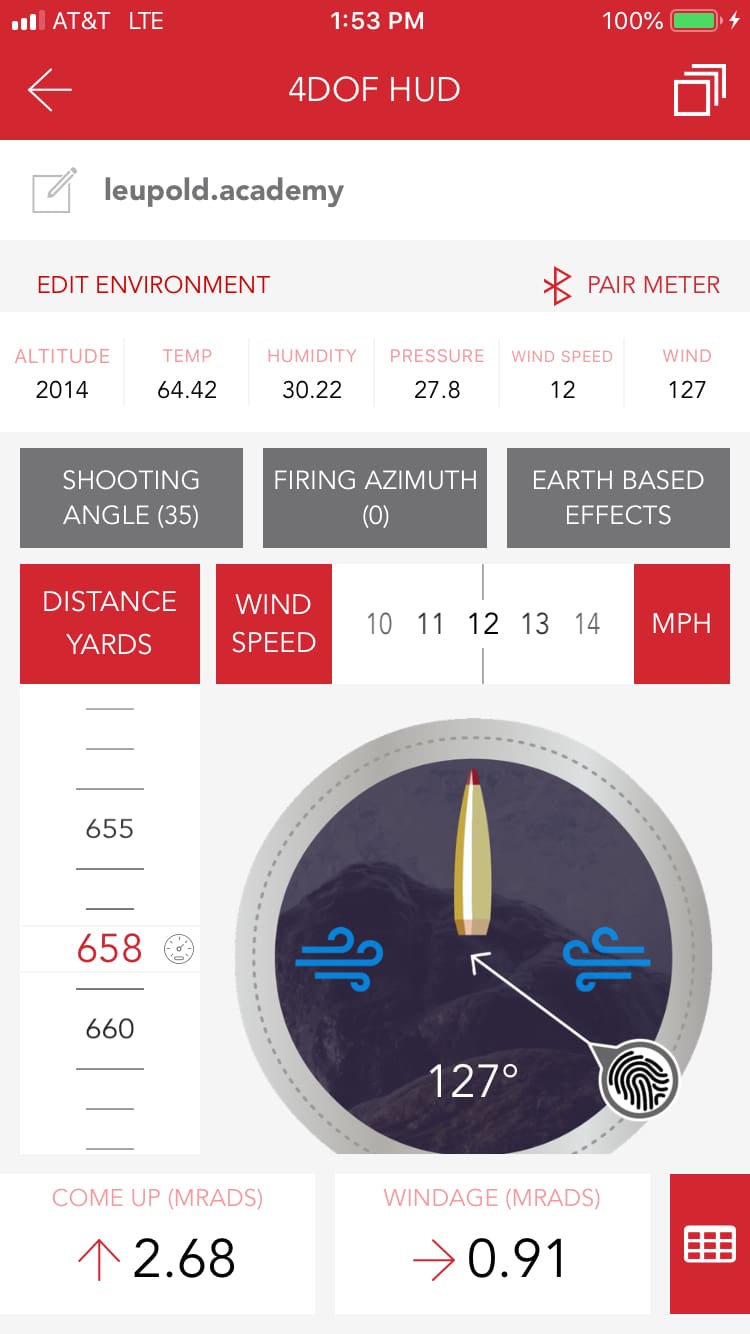
We chronographed our rifles and fed the environmental data into Hornady’s free-to-download 4DOF ballistic calculator app which does its magic based on drag coefficient rather than ballistic coefficient (the same app has a BC calculator, too). Then we got to pulling triggers.
Note: Hornady isn’t selling A-TIP bullets loaded into cartridges. They’re only offering the bullets in quantities of 100, 500 or 1000 for loading. The cartridges we shot were pre-loaded for us by Hornady for our use last week. Hornady has no plans to offer the A-TIPs in loaded cartridges at this time.
Make no mistake…I am not a long-range precision shooter. I’ve shot at distances out to about 1200 yards, but I’m not an expert or competitive shooter. That said, the combination of the A-TIPs and the 4DOF app were enough to get me right on target, right away.
We were dealing with winds that varied anywhere from 8 to almost 25mph depending on the time of day. That obviously made windage…a challenge. But my results were amazing with the A-TIPs and other, better shooters than I had the same assessment.
That said, TTAG’s Jon Wayne Taylor will be doing a much more scientific and complete review of the A-TIP bullets. We have a quantity of 6mm A-TIP and ELD Match bullets headed our way now, so stay tuned for a much more objective evaluation.
I am so stoked about this it is a little ridiculous.
Same.
My better half has gotten to the point of just actively tuning me out when I get started on talking about these.
I’m wondering if the price ends up being a little ridiculous.
Are we talking 10% more than ELD, 50% more, 100% more?
“As you might imagine, all of this makes A-TIPs significantly more expensive. The cost of A-TIPs runs anywhere from 70% more to over twice as much more per bullet over comparable ELD Match bullets depending on caliber and quantity.”
https://www.midwayusa.com/product/1021020278/hornady-a-tip-match-bullets-boat-tail
Midway has it in stock right now (6mm only). 100 rounds of A-TIP = $80. 100 rounds of ELD Match = $36. Price drops to $.70 per round if you buy 1000.
Dang. $0.70 a bullet if I order a thousand. My stoke is somewhat diminished.
Cheaper than most high end lathe turned solid copper bullets, which is what I imagine the area Hornady is targeting.
ELDs were generically 50c MSRP a pill when they released, the relatively recent 147s are 40c MSRP. These A-Tips are generic 70c MSRP, I doubt that once they actually ship the 6.5 135s will cost the same as the 153s, like they do now at midway.
I think if it’s fair to describe VLDs as bullets with better than .950 form factors, then these new class of “ELDs” are bullets better than .875 FF. Up until recently to play in this ballistic realm you had to drop at least $1/bullet on Cutting Edge lathe-turned MTAC solids, and $1.30 and up for MTH fragmenting. But Sierra is already shipping newly factory-pointed bullets like the 183 7mm and 110 6mm, which are competitive with the A-Tip form factors at 50c a round today. I imagine Hornady is positioning A-Tip between the CE MTAC/MTHs and SMKPs price-wise, but that A-Tip will shake out a lot closer to 50c than 70c once it’s been out for a little while.
What I am curious about are terminal effects. The idea that polymer tips act as hollow point expanders has always seemed dubious to me, they’re just hiding a nice flat unjacketed bullet face that can slam open. But I wonder if these aluminum tips actually will act as plugs that mechanically force expansion. If so I doubly want them to put those in a GMX and give the MTH some healthy competition.
TLDR I’m still very much stoked about this entry into the market, but you might checked out the pointed SMKs.
Would have been nice if they made a projectile for .308 Winchester. Last I heard, that was still a pretty popular chambering…
Would you like that in 230 grain or 250 grain?
These are ultra high BC bullets, claiming a 0.442 G7 for the 250 grain.
That’s too heavy for .308. Its intended for .300 win mag.
Not in that competitive environment. I imagine they will put a 30 caliber bullet out in a lighter grain than their initial offerings, but it won’t be their priority.
I’m not getting excited until they come out with some in 338.
Well first, they’ll have to load them up in .260, and then I’d have to find somewhere with a range over 200 yards, and then I might buy some.
Meh. I’ll wait until Brian Litz at Applied Ballistics makes a custom drag curve for them, and can see what their simulator predicts for hit probability at distance. The BC of all projectiles change with velocity. Transonic stability might make a difference….I doubt that the BC will be improved enough over a similar match grade bullet to overcome other factors that determine a successful firing solution enough to justify doubling the price of a bullet.
At that price point might as well go with a machined monolithic copper projectile for about another 15% or so.
I like the idea of getting sequentially made bullets. It might save on the number of projectiles out of a lot that become practice rounds, but anyone looking for precision will still weigh each one before loading anyway.
Thoughts?
Hornady uses Doppler Radar to test bullets out to beyond a Mile IIRC.
In Bryan Litz’s book he notes that Radar is probably the best way to measure a bullets performance.
In fact not long after Hornady started doing it Applied Ballistics announces that they also started using Doppler Radar (the same model Hornady was using) for some of their testing as well.
Of course all of that was after the Applied Ballistics crew bashed and tried to discredit Hornady, tried to smear and discredit Dave Emery and just acted like jackasses because they had competition. A year later they started selling Rifles and Ammo, with custom drag curves for that specific Ammo in that specific rifle using the same Radar Unit that they tried to discredit when Hornady used it, touting advantages that Hornady had discovered at least a year earlier (that each gun will effect the drag coefficient).
It was pretty funny.
Although, I’m less excited about the bullet and just the process, if they could use a similar process on something like an ELDM or ELDX and then sell them as a “select” batch of those I would be interested. Or if any other company starts doing it. One of my gripes with Hornady (other than their long beating lengths) is their inconsistency vs Sierra (who I also have gripes with) coincidentally I think Sierra batches their bullets off of one machine (each machine is a different lot number) where Hornady puts all the bullets from each machine into one lot number. (I could be wrong on that)
How long until 6.5CM drops in price? I recently bought boxes of Federal Fusion 140gr at $1.25/rd and that was on sale.
Was that at a store? Target Sports USA has federal fusion 6.5 creedmoor 140gr for $18, and some stuff was cheaper.
90 cents a round? I bought mine at a Turners…in CA.
Ah, yeah Target sports is an online retailer, local I’m sure they’re a bit higher.
The British actually invented this over 100 years ago. They used aluminum at first then later cellulose and plastic in the tips of their .303 rounds to make them unstable in flesh and tumble and thereby circumventing the spirit of the Hague Convention that banned the use of expanding ammo in combat.
These might make for a hell of a sniper bullet.
SSSSHHHHH!!!!! Saying stuff like that will get them banned.
To the people saying copper, I actually disagree at some level. The reason is that solid copper may just be too dense overall. That means for a specific bullet profile (OAL and ogive dimensions influence BC) you may end up with too much weight to end up with a specific velocity in a specific cartridge. As an example a 308 going from a 165gr bullet to a 208gr bullet has an effect of losing 3-400fps velocity depending on the load. If you can bump the BC of your bullet up while maintaining velocity (within reason) you’re going to do some really good stuff. That’s why the concept of an open, plastic (and now) aluminum tip match bullet even exists is the idea that you can increase the sectional area of the bullet without increasing the weight.
“The reason is that solid copper may just be too dense overall.”
OK, an aluminum core copper bullet, then…
Exactly so:
http://www.cartridgecollector.net/792-x-40-cetme
Too bad the concept never got a chance. But it might yet. The “modern” striker fired semi auto was the way they were first designed, but were abandoned as too unsafe.
Now, a century later, they came back on steroids. The aluminum cored, brass or copper girdled, bullet might could also. Maybe…
I’d sure like to experiment with some in .308 at about 110 grains, but they’d be hard to make in small quantities, and only a handful of the originals still exist, and they’re in 7.92mm anyway.
Lead is used because it’s the densest available material. Copper bullets are either way lighter than lead bullets of the same length, or way longer than lead bullets of the same weight. Long bullets sit deeper and rob more usable powder capacity, but they’re sleeker and may not need to fly as fast to shoot inside a lighter, faster, draggier bullet. That’s the whole balancing act, it’s just that lately all the ballistic projectile advancement has gone into better, longer shapes. So cartridge cases have shortened to accommodate what would have been occupied boiler room anyway: see 6.5CM vs 260.
The thing about A-Tip is that they’re using the length of lightweight aluminum tip to also fine tune the center of gravity of the bullet. I want them to do that for GMX so that Cutting Edge and Barnes get some competition.
Balancing is an interesting premise. Very cool and very good point. It’s not just weight it’s where the weight is. Otherwise hollow base high-vel bullets may be a thing as well which they don’t really seem to be.
I really, really hope they take their new doppler science and A-Tip technology and finally create some GMX VLDs. It can’t be that Cutting Edge is the only company making VLD hunting solids. The 6.5 120gr is their slickest one but still a pig. What gives Hornady?
Aluminium also expands with heat and contracts with cold. Use the following thermal expansion coefficient (λ): µm m-1 K-1. A -20C to a +30C changes length by .003. I know of one data point where a captured bullet exceeded 800° or 426°C.
“I know of one data point where a captured bullet exceeded 800° or 426°C.”
How much of that was aerodynamic heating, compared to friction heating from the rifling lands?
And how much heat was created slowing the bullet down to capture it?
I used Winchester Silvertips years ago, wasn’t impressed, went back to using “The Deadliest Mushroom In The Woods”
Me neither. Too violent expansion. Bullet breakup without penetration to the vitals. The .270Win ones would turn a fox or coyote inside out though. And leave a pelt nobody would ever buy. But I shot a few in the summertime, when the pelts are useless anyway. I still have a few of those from the 1970s around.
OFC, the old WinSTs were just a jacketed lead core bullet with an aluminum tip to help feeding in the then-new semi auto rifles. Nothing like these Hornadys. I doubt if the Winchester tip was machined. Likely swaged.
Anybody really knowledgeable about the construction of the old Winchester Silvertips know the answer? I’ll bet DG does, if he’s listening…
I know I’m being a bit pedantic but, if the bullets are more consistent in weight, then this statement is incorrect.
“Hornady, however, packages A-TIP bullets sequentially. That means far more consistency and a much flatter bell curve.”
High variability causes a bell (or normal) curve to be more flat, high consistency (low variability) results in a sharper curve. More data points closer to the mean means a narrow, steep “bell” not a wide flat one.
Not to mention that variability in manufacturing comes more from tolerances in the tooling than any other factor. Thus the only variation that packing them in sequence will effect is the change in tolerance as the machine tooling grows older and gets more worn. This will be extremely tiny over a few hundred rounds, and would only likely even be measurable from a bullet made on a certain machine today, versus one made on the same machine a year from now.
Packing them in sequence, versus packing them in lots, it would only be possible to achieve the tiniest of improvements, nowhere near the marketing claim of: packing “A-TIP bullets sequentially. That means far more consistency”.
No, it doesn’t. It means the tiniest of improvements that even the best shooter won’t see at a thousand yards. The machining of the tip, instead of casting or swaging it, will improve consistency many times more than just keeping the bullets together in their order of manufacture. But I guess some marketing genius decided that people could understand packaging better than machining (or maybe that the packaging is more “sexy” than manufacturing processes), so they decided to emphasize that, instead of what might actually make a measurable difference.
And this doesn’t even mention the known fact that the base of a projectile is the ‘steering’ end. The tip is more for ballistic coefficient than it is for consistent groups.
Just go try this out for yourself. Take some ammo out to the range and shoot it for group. Take some of the same ammo and file a diagonal cut across the bullet’s tip. Now shoot that ammo the same way, and take note of how much the group opens up. It will be minimal, and the filing has changed the CG and BC hundreds of times more than any manufacturing tolerance, even if the bullets in question were made by Hi-Point.
Yes, I know Hi-Point doesn’t make bullets. It was just a simile to illustrate the cheapest possible manufacturing. Nothing wrong with Hi-Points, just like there is nothing wrong with the projectiles that one just messed up the tips of with the file. They will still shoot fine(not as good as before, but minimal change) just like Hi-Point firearms do. They will LOOK terrible(again like a Hi-Point), but still function.
There is a definite change in point of impact when the tips of my accubond or Amax bullets are deformed. There is even a change in point of impact in my bullets that have a wider meplat than the others in the same box.
Inconsistent inputs result in inconsistent output.
But by HOW MUCH, did you see those groups open up when the tips were malformed? Note that I said; “minimal” and NOT; “non existent”.
I’d be extremely surprised to see it even go as high as 10%. That’s all I ever managed to get when I first proved this issue to my satisfaction decades ago.
By way of contrast, try just the tiniest swipe of the finest tooth file you have on the base end, and then watch them not even hit the paper. The base end is hundreds of times more important (to external ballistics) than the tip of the projectile.
OFC you understand that I’m not advocating filing off the tips of your bullets to make some imagined ‘improvement’! I’m only pointing out the differences between deformed bases and deformed noses, relative to each other. The more consistent EVERYTHING is, the better the groups will be. Naturally.
The question is: where is the MOST improvement in consistency readily (or not so readily, when one gets down to only the smallest of improvements) available under a particular system? On the projectile, the tolerances on the base are much more important than on the nose. In the realm of manufacture, the construction of the nose is more important than the packaging. Etc.
But on a whole new system? That’s a whole new story. A long, high BC, aluminum core projectile with a brass girdle around its middle? That’s a whole NEW system, and potentially a much better one. Although only for extreme ballistic performance at long range, the current fad. It stands to reason that such a bullet would have less terminal ballistic performance than a lead core projectile, thus meat and trophy hunters would likely still prefer a lead core bullet.
Long range hunters of varmints and such, OTOH, would likely prefer the better external ballistics, and not care much, if at all, about the decrease in terminal ballistics.
Actually yeah, I think we are in agreement. When I was thinking about my groups I was thinking about my 300-yard groups in which I can easily tell which round was malformed. That’s probably around the quarter of an inch mark. Of course, that’s not taking into account tips that are bent or are otherwise significantly damaged.
When I am thinking of the use of these bullets, and how I use them, I am not thinking of the differences at a hundred yards, but at 500 to 1000.
OFC I never insinuated that you should deform the bullet tips on purpose and anticipate an improvement. Only that deformation in other areas will yield more inconsistency. And also that the long range improvements of these bullets will be due more to the machined tip, and not the sequential packaging.
You can prove this to yourself also. When you get the shipment for testing, just take the first one or two out of each package, and then load and test these for group, just as you will the rest, but keeping the results separate.
Test these individual bullets, now out of sequence, and compare these groups to those you are able to achieve with the other ones loaded in sequential order. Note any differences you find in the mean value. If you can find a measurable difference at 500 yards, I’d be surprised. I would bet a rather large sum that you will NOT find “far more consistency “, which is the claim. Or likely any measurable gains at all.
Note that I DID NOT say these bullets will not perform to a higher standard. What I DID say was that the ones loaded out of sequential order will not show a measurable difference vs. the same bullets loaded sequentially.
I’ll be looking forward to seeing the results of that test. You might actually see a couple thousandths of an inch at 500 yards, but I doubt it. You will need a few groups, enough to get a decent mean average. I predict the average spread between groups to be many times the difference between the ones loaded sequentially and those not.
Not to throw a wet blanket on everyone’s parade, buuut…. Aluminum tipped bullets aren’t exactly a new idea…
https://picclick.com/old-Winchester-Silvertip-32-Winchester-Special-Super-Speed-202716633369.html
Aluminium tipped bullets aren’t new, but the link you provided isn’t the same kind of thing at all.
Yeah, I covered that in two other posts up above…
You covered that the link that you provided is about bullets that are nothing like what we are talking about here, or you covered that aluminum tip bullets are nothing new? Did a post of yours get deleted, because I’m not seeing that.
OK, here they are again:
http://www.cartridgecollector.net/792-x-40-cetme
https://forum.cartridgecollectors.org/t/7-92×40-cetme/27357/25
https://www.youtube.com/watch?v=3Njddshr3n8
etc. just search “7.92 cetme” for more.
You also might try looking under MyName’s post. My responses about manufacturing, etc. are there under his post.
Hornady has been making aluminum tipped bullets for years.
Of course they’re not claiming that the idea is new, they’re saying hey heres our new lineup of bullets.
Here’s another “new” bullet idea that’s quite old:
https://www.youtube.com/watch?v=3Njddshr3n8
The Cetme 7.92X41 got caught up in the US demand that all NATO members adopt the 7.62X51, and so it never really had a chance, but I think it was a concept worth further development. Unfortunately, it never got the chance.
I think this concept could make a big splash in today’s long range shooting fads, but in a smaller diameter and a better case. One could still get the high BC, but on a much lighter projectile, with the corresponding higher velocity and lighter recoil. Unfortunately, these bullets would be very hard to make in a small shop, otherwise I’d have been experimenting with them years ago. But made in quantity they wouldn’t likely be any more expensive than these Hornadys at almost a buck each.
The price might seem high compared to other Hornady offerings, but check prices of Berger, Barnes, Speer, heck even some from Sierra and Nosler are comparable.
Some of the BCs on these seem a bit optimistic. I’d like to see some honest, independent testing. Unfortunately, almost all of the articles I’ve seen on the A-Tips are more keen to sell the product than put it through the ringer and verify that it lives up to the hype.
Also curious what cartridge is capable of pushing the 250gr .308″ bullet at a high enough velocity to achieve the published coefficient (guessing it’s for the .300 PRC, though I figure the .300 NM would also work).
I’m hoping they release a .338″ version, or maybe even a .375″ for the CheyTac.
I just about lost it after the 4:55 mark.
As the gentleman is lovingly caressing his bag:
“They will never be cleaned. You might even see there’s a little grease on there … feel good about what you’re doing, and get excited … because these things are gonna just scream ‘performance’, and they scream ‘sexy’. When you look at ’em, you just smile.”
Thanks for the laugh, VP Jason Hornady.
I would be interested to see if this approach to bullet manufacturing could be used to produce a bullet with a tungsten tip. Why tungsten….because I think that if the CG of the bullet was moved forward (tungsten is almost twice the density of lead) lower twist rates would be needed to stabilize an otherwise identical projectile. Actually, if more of the front of the bullet was tungsten the weight increase might be enough that on solid copper bullets the length could be decreased quite a bit (the main problem with copper is the extra length for same weight as lead). Lower twist rates would mean more velocity, if all other factors were unchanged. Cutting Edge would be the perfect company to try this out, they already turn solid copper bullets and build them with special tips.
Comments are closed.